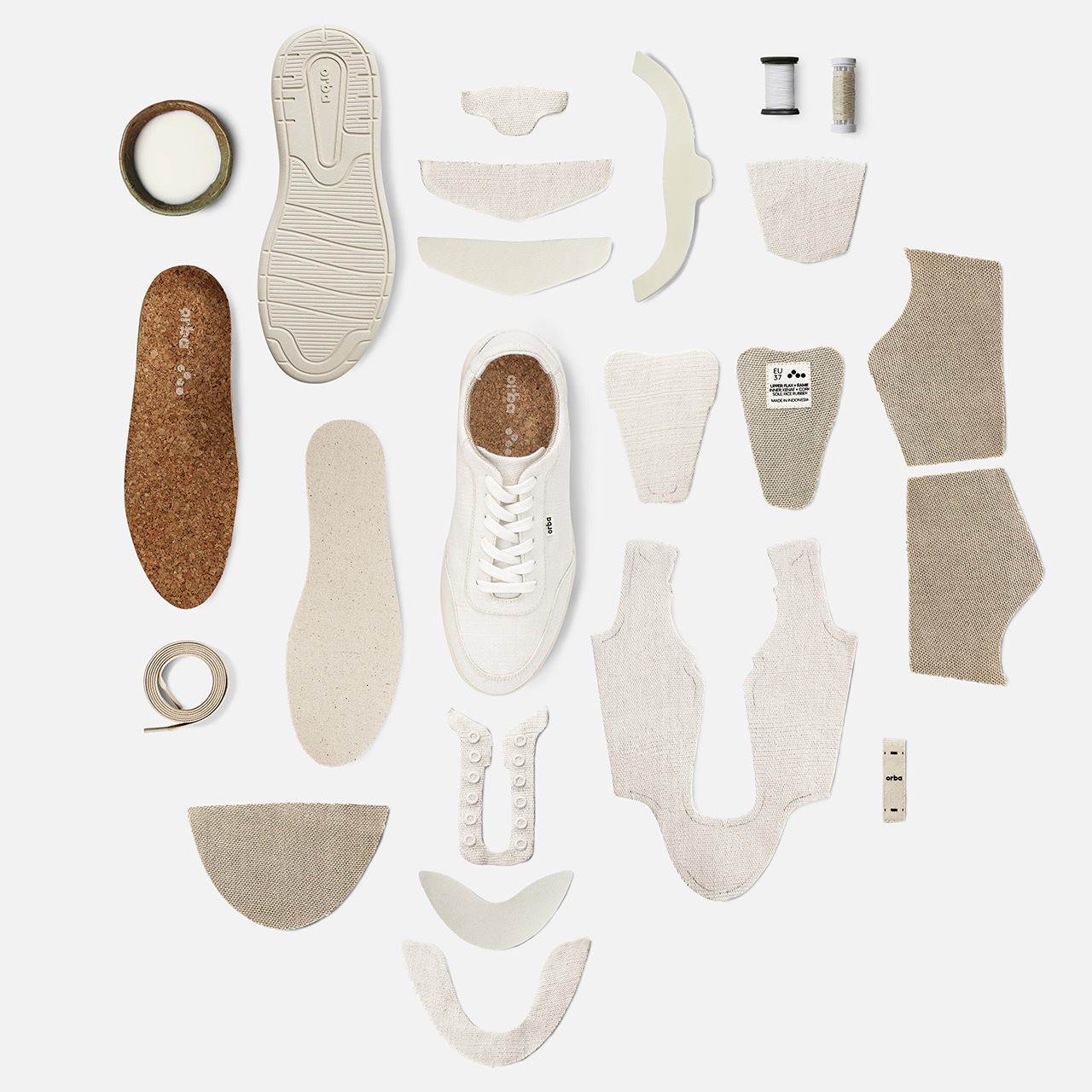
Designed in New Zealand & crafted from some of the most highly renewable plant-based materials in the world.
All components and materials are designed and crafted from plant-based materials and meet the relevant ISO standards for casual footwear including abrasion and slip resistance, flexibility and tear strength.
All are tested for pollutants so that the shoes meet the level required for certification. This assures us that our shoes are as safe as possible.
Sole
A world-first compound, over 93% plant-based, also with around 4% beeswax and a less than 2% trace of other natural compounds and minerals for durability, comfort, performance and appearance.
-
Natural Rubber
-
Rice Husk
-
Coconut Oil
The Orba sole is designed to biodegrade, but only when you’re ready, after the useful life of the shoe. As with all things, biodegradation occurs only in a suitable micro-organism rich environment, and then the sole will break down at its own pace.
Traces of titanium dioxide and zinc, naturally occurring compounds that are also used in sunscreens, are necessary to help with colour, colour fastness and UV resistance are not biodegradable, and delay the ability of the sole to start to degrade during the life of the shoe.
Beeswax, which is biodegradable, and traces of pine resin and sulphur, which are natural preservatives and are not biodegradable, are added improve the performance of the sole during its usable life.
The coring in the forefoot is moulded in a lateral wave pattern to allow that part of the sole to curl with the forefoot and provide cushioning in the lengthwise and vertical planes. The crosshatch coring at the heel allows minimal flex, and more limited vertical cushioning. These structures reduce the weight of the shoe and add to the comfort, because each part acts as a shock absorber, working in tandem with the Insole.
Collapsible content
Smoked Natural Rubber
In comparing the natural rubber in the Orba soles to the most common synthetic material - styrene-butadiene rubber (SBR), we calculate that our natural rubber will reduce CO2 emissions by 2.6kg (52%) and fossil fuel consumption by 87.3MJ (77%) per kg of material.
Smoking, using wood waste from natural rubber forests, is a natural preserving process that also increases the hardness and durability of the natural rubber, and therefore the performance of the shoe.
Rice Husk Ash
Orba soles use Rice Husk Ash as a “Biosilica” instead of using mined Silica. Rice Husk is a bi-product of rice production that usually goes to waste. Synthetic rubber production uses Silica sourced from quartz rock mining.
As a result rice farmers can earn additional income, and this brings social and economic benefits to farm communities. Biosilica use reduces the demand for resource intensive quartz mining and reduces the pollution that results from mining.
Coconut Oil
Coconut oil is used in the place of petroleum-based oils. It further improves the sustainability and performance of our natural rubber over that made from synthetic based compounds with no compromise of quality.
Our research shows that our use of Coconut Oil brings better strength and improves abrasion resistance over petroleum based compounds.
Beeswax
We are using this essential and natural bi-product of honey production in the place of synthetic alternatives. It helps our other natural components to combine into a high performing compound.
Honey cannot be collected without also collecting beeswax. It is a natural bi-product of honey production. Our research indicates that beeswax is more sustainable that other natural alternatives to petroleum-based paraffin waxes that are used in synthetic rubbers.
Beeswax is around 2% of the shoe by weight, and is the only animal based product that we use.
Other Compounds
A small amount of pine resin, the gum-like discharge from various species of pine tree, a trace of sulphur, and traces of zinc and titanium compounds (as used in sunscreens), are used in the sole to improve the performance and wearable life of the shoe.
These are all naturally occurring compounds that are non-toxic and are environmentally safe. They are under 2% of the shoe by weight. These compounds are not biodegradable.
Upper
Three of the most highly renewable plant materials in the world combine into a unique natural upper that offers performance, comfort and durability equivalent to or better than all alternatives.
-
Flax
-
Kenaf
-
Ramie
Flax, Kenaf and Hemp fabrics all allow the foot to breath naturally. They all absorb moisture and resist bacteria and fungi, which is important for footwear as it reduces odour and aids good foot health.
All are renewable crops, able to grow to harvest in a few months, in poor soils without fertilizers, pesticides, or irrigation. Rain water is enough.
Collapsible content
Flax Canvas
The Flax Canvas outer is hand woven from bleached yarn by master weavers using traditional looms.
The natural yarn varies in its thickness and thinness. This creates a fabric with a special character and a slightly uneven style. It is a durable fabric that wears well, resists stretch and maintains its shape well for the life of the shoe.
There is evidence of Flax fibre being used 30,000 years ago. Our Flax, grown in France since before the Middle Ages, is one of the world’s most sustainable crops. It grows very quickly, ready for harvesting 100 days after planting. The plant craves carbon dioxide. It absorbs a huge amount, turning it into oxygen.
Flax Canvas won’t rot in water but it will biodegrade in a year or so in the earth in the presence of the right microbes.
Our Flax Canvas production generates next to no waste. We only use the fibre, but every other part of the plant is used in other products, from health food supplements to natural cosmetics, because the oil smooths, protects and conditions the skin and hair. This indicates the safety of products made from Flax.
A Life Cycle Analysis to compare the sourcing of flax against traditional leather indicates that flax decreases CO2 emissions by 29.2kg (88%) and reduced water use by 20m3 (91%).
Kenaf (Hemp)
The Kenaf Hemp liner is spun and woven with techniques that create a fabric of special softness, equivalent to premium linen. This enables Orba shoes to be worn without socks for light wear.
Like its cousin, Industrial Hemp, Kenaf fabric is a good thermal insulator. This helps to maintain foot warmth in cool weather and cooling in hot and humid weather.
Kenaf grows quickly, is ready for harvest in 4 – 6 months, and it is produced in the same area as our factories reducing our transport miles.
Kenaf plants absorb C02 at three times the rate of equivalent trees. This means, even after processing the carbon footprint of the fabric is nearly zero. We expect Kenaf harvesting will generate wealth in local communities, contributing to the social and economic development aspects of sustainability.
Ramie (Nettle)
Ramie backing is tightly woven into a fine light-weight stiffener and used to reinforce the durable flax outer and the soft kenaf liner.
A layer of ramie is laminated to each of the flax outer the kenaf liner. This improves the shape-holding and reduces the wrinkling often found in non-reinforced canvas style uppers. The triple combination of flax, kenaf and ramie creates a fabric that has performance equivalency to leather, but with strong natural character while minimising the negative impacts of leather and the other alternatives.
The ramie plant has been used to make fabric for more than 6,000 years. We use traditional methods to create a fine backing fabric that is 100% natural, is more absorbent and stronger than cotton, breaths well and is naturally resistant to bacteria and odour.
Ramie is part of the thistle family, and grows like thistle too, able to be harvested up to 6 times per year.
Footbed
Shaped and compacted into three layers, each designed to provide the ergonomic support appropriate for each part of the foot.
-
Cork
-
Coir
-
Agave Sisal
Designed for a firm durable feel, the footbed maintains its overall shape while also allowing appropriate compression in the heel and forefoot sections, allowing those parts of the footbed to adapt to the shape of the foot with wear, bringing increased comfort over time.
The materials are reasonably breathable and light, and as with all main components, have natural microbial and fungal resistant properties while still being biodegradable. They have good shock absorbing characteristics, good thermo-insulation for hot and cold temperatures, and as with the fabrics in our upper, they help draw but do not retain moisture, which is important in hot or humid conditions.
The footbed is designed to be easily removable, which is important because it helps with cleaning and drying the shoe, and allows the shoe to be aired after wear and in storage.
All footbed components are renewable resources with low environmental impact. The require minimal land and very little water when grown using sustainable practices. They are all sustainably and ethically sourced and manufactured.
Collapsible content
Cork
Cork is compressed and used only in the top layer in the footbed. It has both elasticity and about 85% shape memory. This means it will recover most of its shape after being compressed during wear and will not lose shape over the life of the shoe. But it will mould slightly to individual foot shapes with wear, increasing the comfort of the shoe over time.
Cork comes from the bark of a particular type of oak tree. The bark is harvested every 7 years, and then it grows back. Harvesting does not harm the tree. The harvested trees even absorb far more CO2 than unharvested trees, and the trees are producers of oxygen. Cork is a 100% natural, sustainable, renewable material that biodegrades completely.
Coir (Coconut Husk)
Coconut husk, which is most of the two lower layers of the footbed, is a very strong fibre with excellent wear resistance. It improves the durability of the insole, but still has enough flexibility to bend with the shoe while also lending a firm level of shock absorption.
Coir is a bi-product of the production of coconut products, just as rice husk is a biproduct of rice production. It is from the fibrous inner part of the coconut that is often discarded as a waste.
Agave Sisal
Sisal is included in the bottom layer of the footbed heel section as a reinforcing agent, to strengthen the heel section. This fibre is course and inflexible, enabling this section to be built up in height, improving the ergonomics and durability of the shoe.
The plant is a woody succulent native prolific to Central America, and used there as source of fibre for rope since before the 14th century.
Latex
Latex, the sap of the rubber tree, is used as a natural adhesive and combined with the Coir and the Agave Sisal in the bottom two layers of the insole.
Components
Collapsible content
1. Water-based adhesive and primer
Water based glue is used to laminate flax and ramie together for the outer, and Kenaf and Ramie sheets for the inner.
The completed upper is stitched into one piece, and then bonded to the sole after both parts are cleaned and etched with a water-based primer.
The use of the primer and adhesive in the thinnest possible layers causes the components to combine with a better direct bond. This kind of bond is strong and long lasting, and loads are dispersed across the entire bonded surface without the individual stress points found in poorly stitched shoes.
Our tests show the strength of the bond in our shoe exceeds the ISO standard.
The adhesive will be elastic for the life of the shoe and will not become stiff, allowing the shoe to flex with the foot. This is important for long term comfort.
This extra testing is required because the adhesive is a manufactured product, not a natural product and not plant based. There has not as yet been a plant-based adhesive available to us that is strong and flexible enough, would last the lifetime of the shoe, and will also biodegrade.
2. Open cell natural rubber foams
An elastic open cell soft foam in the collar pocket improves top-of-heel and ankle support and reduces friction and the chance of blisters.
The foam, less than 1% of the shoe, is made from a compound of 80% natural rubber and 20% synthetic rubber, air blown to form this light weight material.
The 80% natural rubber is sustainably harvested from the sap of the rubber tree. It is biodegradable.
The synthetic rubber, less than 2/10ths of 1% of the weight of the shoe, to enhance the elastic properties of the foam. This component in the foam is not biodegradable. We are working to find a replacement to this component.
3. Certified organic cotton laces with cellulose aglets
Orba’s laces were created for their natural matte look and for their quality. They firmly hold the entire top of the foot with comfort without pressure points.
They are “grippy”, and this minimises slippage and means double knots and jams should be unnecessary. The laces grip the eyelets well, and this helps adjust the mid-shoe to the shape of the entire top of the foot. This is important for foot comfort.
GOTS (Global Organic Textile Standard) certified cotton was chosen for the laces because it can perform better as a shoelace material than any other natural alternative.
Cotton as a crop does rate less highly in sustainability terms than Flax, Ramie and Hemp. But braided cotton offers greater strength and the right amount of elasticity, which is important for laces. GOTS certification means our cotton is grown and processed using the best practices toward sustainability, including the elimination of pesticides and poisons, the minimisation of water use, and assurance of fair trade and labour practices.
Our GOTS Certified Organic cotton laces are 100% plant based with no additives, and are 100% biodegradable. They are better in sustainability terms than alternatives made from recycled synthetics and plastics. The recycled materials reduce pollution, but are further away from eliminating it than our natural products.
Cellulose Acetate Aglets at the ends are needed so the laces can be threaded through the eyelets more easily, and to prevent fraying.
Cellulose is formed in the cell walls of green plants. It’s a waste bi-product from agricultural production, made into a transparent bio-plastic film that is naturally slightly adhesive.
Our Cellulose Acetate has Oeko-tex Standard 100 certification and is 100% biodegradable.
4. Bio-plastic reinforced heel counter
They are “grippy”, and this minimises slippage and means double knots and jams should be unnecessary. The laces grip the eyelets well, and this helps adjust the mid-shoe to the shape of the entire top of the foot. This is important for foot comfort.
Bioplastics are made from vegetable starch, the essential material that carries nutrients in plants. A small amount of this stiff, thin, resilient material is heat moulded so that it bonds into a pocket in the flax outer. This improves the strength, comfort and durability of the heel and toe of the shoe for its wearable life.
The bioplastic in Orba shoes does not compromise performance when compared with fossil fuel based and synthetic plastic alternatives. But in 2021 only around 1% of the plastics produced worldwide are bio plastics. We would like to see this percentage grow.
Our bioplastic is certified to fulfil the biodegradability requirements of EN 13432 and ASTM D 6400. This means it will meet the ISO 14855 standard to which we have designed the shoe. It is 95% made of biodegradable plant-based polymers and 5% biodegradable natural cotton. It’s a renewable product. Our supplier’s production processes are solvent free, produce zero waste water, and they have a waste minimisation plan in place.
5. GOTS certified organic cotton threads & labels
GOTS (Global Organic Textile Standard) certification means the cotton has been ethically and sustainably sourced from the farm through to manufacturing. All farmers, processes, workers are safe from harmful practices. Soil integrity is protected, and water-used in production is minimise. The cotton is safe from harmful additives and toxic pesticides.
Cotton in general is natural, renewable, plant based, and 100% biodegradable. But is has more environmental impact than Flax, Kenaf, or Ramie. Uncertified cotton may be using large amounts of water and pesticides.
Our use of GOTS certified organic cotton wherever possible ensures that these environmental impacts are minimised.
We use the heaviest certified organic cotton thread that is available. Its strength is needed to match the strength of the woven Flax Canvas. Three threads are braided into a 3-ply thread that is strong, but not so heavy that it won’t run easily through the sewing machines and make our worker’s jobs harder.
By using this method we achieve better strength and durability than if we used alternative flax or hemp threads. The overall performance is equivalent to the synthetic threads, but without the environmental costs.
The fine certified organic cotton thread for the labels is dyed before weaving in process called dope dying. This is more environmentally friendly than alternative processes. The thread is then woven to size, hemmed, and printed with inks that are safely non-polluting.
Eyelets are embroidered with a heavy thread. While this can cause the laces to grip the eyelets firmly, it is important as it avoids the use of metal or synthetic eyelets while still reducing wear and fraying.